SGM LIBS* Powered by CLEANSORT
THE GAME CHANGER IN LIBS METAL SORTING (Laser Induced Breakdown Spectroscopy)
The Technology: LIBS Laser Induced Breakdown Spectroscopy
Laser-Induced Breakdown Spectroscopy (LIBS) is an advanced laser technology used for the analysis and identification of metal pieces in their different chemical compositions and alloys. A LIBS sorter fires a high-energy laser pulse onto the material’s surface. The pulse creates a microplasma, whose emitted light characterizes the chemical composition of the metal in its different elements and is analysed by sensors performing a few milliseconds breakdown spectroscopy.
LIBS is a complementary technology to X-ray transmission, which does not perform any chemical breakdown analysis but sorts metals and metal alloys based on their different densities.
LIBS is also a complementary technology to X-ray fluorescence, which also performs a chemical breakdown analysis but presents limitations in performance on light metals like Magnesium and
Aluminium alloys because of the low energy of the light they emit under the XRF source.
Although LIBS can do what XRT and XRF do, those technologies are complementary to LIBS because the capital cost of a LIBS sorter on a per-ton-per-hour capacity is quite higher than that of XRT and XRF sorters, making the cascade of those different technologies a more convenient solution.
THE ADVANTAGES OF THE SGM-Cleansort LIBS SORTING TECHNOLOGY
The game changer
LIBS is a surface analysis technology which requires the surface of the piece to be cleaned of contaminants such as paint, dirt and oxidation to be able to perform an accurate reading.
The game-changing advantage of the SGM Cleansort LIBS sorter lies in its material cleaning process, which consists of its proprietary laser square surface ablation process. This advanced cleaning method ensures thorough surface preparation for every single piece by removing surface contaminants before analysis, enabling the generation of spectra that accurately reflects the material’s chemical composition.
Alternative solutions consist in either performing multiple laser burning spots along each piece (multi-spot analysis) or performing repeated burnings on the same spot (multiple single-point burns) to gradually remove surface contaminants. In the first case, you hope to find at least one sufficiently clean spot, and in the second, you generate an accumulation of burning residue around the edge of the cone spot, which can interfere with the spectroscopy reading.
Those two alternatives are not suitable nor well performing as material surface cleaning solutions, especially when considering contaminants like paintings that can be 70 to 120 microns thick, as with aluminium bodies in the automotive industry.
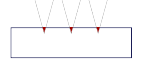
Analisi multi-spot
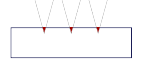
Analisi multi-spot
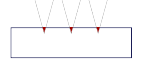
Analisi multi-spot
True quantitative analysis vs qualitative analysis
A superior material surface cleaning process makes possible the production of high-definition spectra which shows accurate breakdowns of the chemical composition of every single piece and allows for doing a quantitative analysis of the material. Low-definition spectra that does not provide detailed chemical breakdowns of the material composition only allows for qualitative analysis where sorting is based on predefined criteria (e.g., max Si, max Mg), determining whether each individual piece meets those thresholds.
Running quantitative analysis results in disposing of quantitative information of both the eject and drop streams of the material which enables customers to make more informed decisions and optimize production, quality, and value of their aluminum scrap.
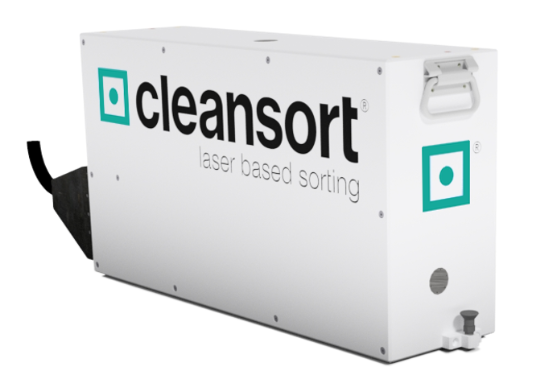
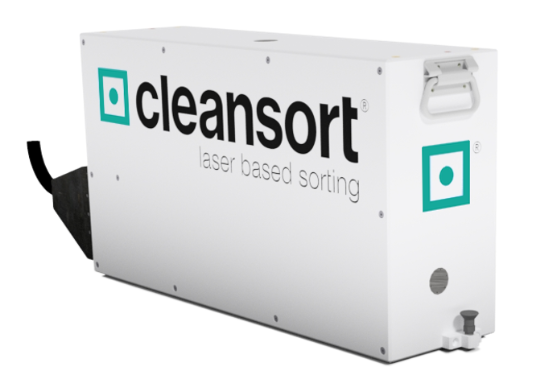
Dynamic data computing process
A qualitative analysis only allows for a Yes/No static sorting decision on an individual piece basis. A quantitative analysis allows for taking advantage of the chemical composition of all the pieces processed before, while running a proprietary dynamic computing data process where the sorting decision is based on whether or not the average of the chemical composition of all these pieces fall within the threshold.
Making sorting decisions based on a dynamic computing data process results in higher recoveries, which can be up to 1.5–2 times what can be achieved with static sorting, as, in the end, what matters is not the single-piece sorting but the melt analysis of the complete batch.
Versatile material analysis
The wide measurement spectrum of the SGM Cleansort LIBS sorter allows to easily switch between different materials. With a simple approval and calibration process, the sorter can pass from sorting non-ferrous metals to steel.
Modular solution and high capacity
The SGM Cleansort LIBS sorter is designed as a modular solution, allowing different laser ablation and reading modules to be mounted on the same frame. Configurations range from 3 to 6 modules, with a conveyor belt width of 720mm | 28” up to 1440mm | 56” enabling throughput capacities between 5.5 and 11 tons per hour for aluminum scrap in the 30 to 120 mm | 1¼”–4” size range considering an average weight per piece of 34 grams (0,075 lb).
This scalable design allows for an initial investment in a sorter with fewer modules, with the option to increase capacity over time by adding additional modules to the existing sorter frame.
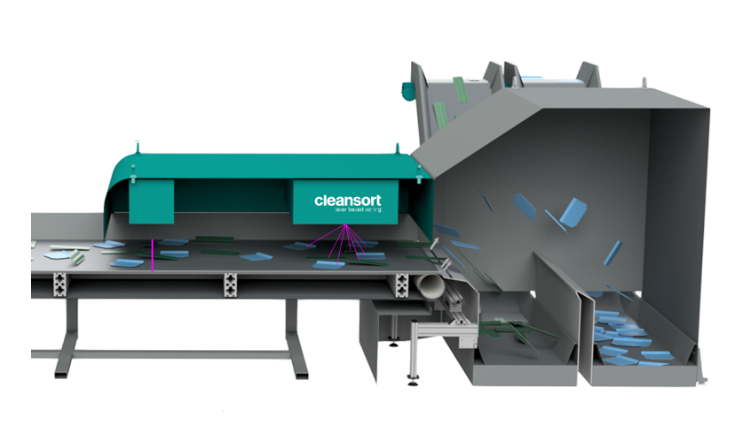
STATIC AND DYNAMIC SORTING
The SGM Cleansort system offers two advanced sorting options while delivering accurate information on the chemical composition of both ejected and non-ejected fractions:
Static Sorting:
This traditional method analyses each individual piece and makes a yes/no sorting decision based on whether its chemical composition meets customer specifications.
Dynamic Sorting:
Thanks to our proprietary dynamic data computing process, the dynamic sorting feature evaluates the individual composition of multiple pieces at the same time and makes the sorting decision based on the average chemical analysis of those pieces. This can boost material recovery up to 1.5-2 times higher than static sorting.
By combining these two options, the SGM Cleansort LIBS sorter delivers unmatched flexibility and efficiency in scrap sorting.
MATERIAL PROCESS
Material feeding and preparation
Metal scrap is conveyed by vibrating feeder to the belt of the sorter running at up to 3 m/s.
Capacities on aluminium scrap with a size fraction of 30 to 120mm | 1¼”–4” range from 5.5 to 11tph (based on average weigh per piece of 34 grams (0.075 lb)).
High-speed laser scanning
As the scrap moves along the conveyor, high-speed 3D laser scanners measure the surface and geometry of each piece and direct the LIBS laser on the X/Y coordinates of the piece and adjusts the auto focus to its Z-axis.
Laser cleaning and analysis
Once the X/Y/Z coordinates are set, the Cleansort module performs two key functions:
- Laser Pre-Ablation:
The system cleans the surface by removing contaminants, coatings, or rust, exposing the underlying material for analysis. - LIBS Measurement:
The laser induces a plasma on the surface of the material. Doing the breakdown spectroscopy of the plasma, material is identified in its exact metal composition, distinguishing not only between metals like steel and copper but also between alloy groups, such as 5000 and 6000 series aluminum, and even between similar alloys like 6010 and 6016.
Sorting and output
After analysis, the system uses advanced air pulse technology to separate material in different composition streams.
Each LIBS module analyzes an average of 15 pieces per second, resulting in 60 pieces per second for a sorter provided with 4 modules and 90 pieces per second in the case of 6 modules.
THE NEW FRONTIER IN ALUMINUM SCRAP PROCESSING
Boost the value of your aluminum scrap by efficiently segregating different light aluminum alloys (e.g., 6xxx from 5xxx, 6060 from 6082) to be sold as premium furnace-ready products.
- Superior Cleaning
The surface laser pre-ablation cleaning process offers better cleaning compared to multi-spot burns or multiple single-point burns. - Increased Capacity
The modular configuration allows for the installation of 3 to 6 laser modules on the same sorter frame, either from day one or as your needs grow. This scalability enables capacities ranging from 5.5 to 11 tons per hour for aluminum scrap (> 1¼”–4”). - Higher Value per Ton
Innovative data analysis and computing process offers the option to optimize the material sorting even further by creating a product that is as close as possible to the desired alloy composition. This new approach can potentially double the added value of your sorted material. - TEST US NOW
Test the performance of our sorters with your own material.
Our worldwide team is ready to answer your questions and collaborate with you to identify the optimal sorting solution for your needs. - Notes:
- “Plug and Play*” configuration indicates that the system is ready to be installed and used without further complex configuration.
- Throughput capacity may vary depending on material type and power specifications.
Modelli
Modello CleansortR | Quantità Moduli clean2sort | Throughput Stimato (Peso medio pezzo 34 g) | Configurazione |
---|---|---|---|
CleansortR 720 | 3 | 5,5 t/h | Plug and Play* |
CleansortR 960 | 4 | 7,0 t/h | Plug and Play* |
CleansortR 1200 | 5 | 9,0 t/h | Plug and Play* |
CleansortR 1440 | 6 | 11,0 t/h | Plug and Play* |
Notes:
-
- “Plug and Play*” configuration indicates that the system is ready to be installed and used without further complex configuration.
- Throughput capacity may vary depending on material type and power specifications.