Our name and logo reflect our first two historical core businesses: lifting magnet systems for the steel industry and separators for the recycling industry.
Over the years, SGM has established itself as a pioneer and leader in industrial lifting magnets and has expanded its magnetic separation expertise to include other in-house separation technologies, such as inductive-based sensor separators, X-ray separators, color sorters, gravimetric separation, and complete process plants.
With multiple subsidiaries worldwide, we leverage our proximity to customers and cutting-edge technologies as our key strengths, giving them a solid reason to rely on SGM.
Separation: Our Mission
Our ambition is to contribute to the circular economy by helping our customers recycle more efficiently and effectively while enhancing their profitability.
Lifting: Our Mission
SGM is committed to promoting the use of advanced lifting magnet technology worldwide, ensuring maximum safety and productivity in steel handling operations at steel mills, steel service centers, ports, shipyards, and any location where heavy steel loads are managed.
Values
Expertise
Because nothing is more important than learning through experience. Founded in 1954, SGM offers one of the largest and most internationally recognized portfolios of references in its field of expertise.
Innovation
This is the driving force behind our growth and expertise. SGM offers the widest range of in-house designed advanced technologies for both lifting and separation applications.
Trust
Trust is the starting point of every collaboration which we pride ourselves in continuously strengthening over the years.
This special bond we have built with our customers is confirmed by the size and prestige of our references which keep coming back to us.
Passion
Our passion for what we do drives us to stay close to our customers’ needs and continuously seek the latest and most advanced innovations.
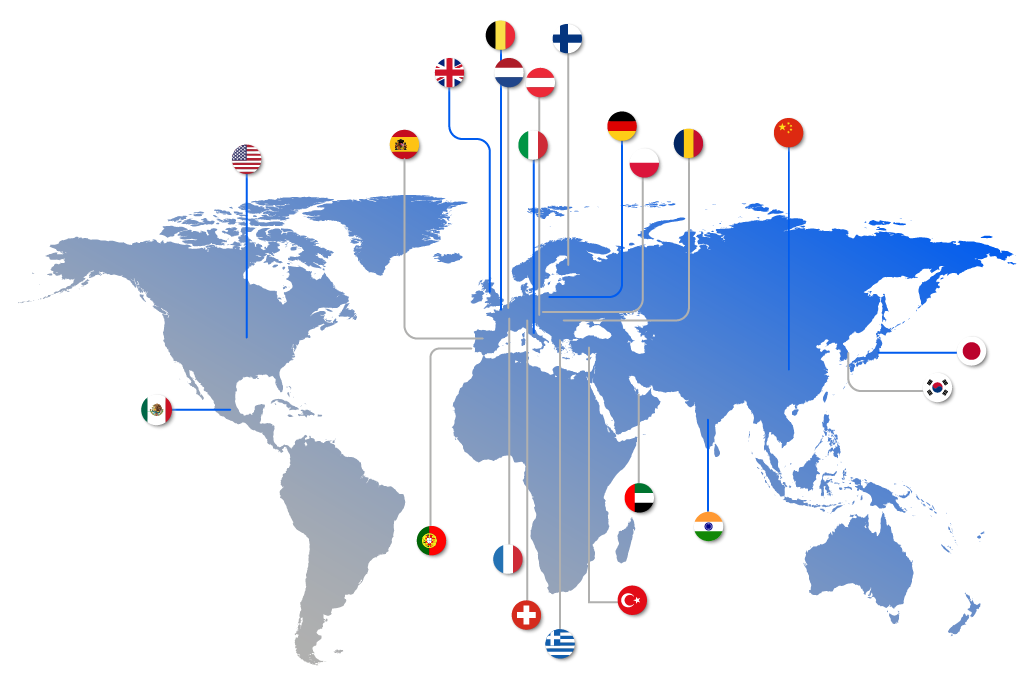
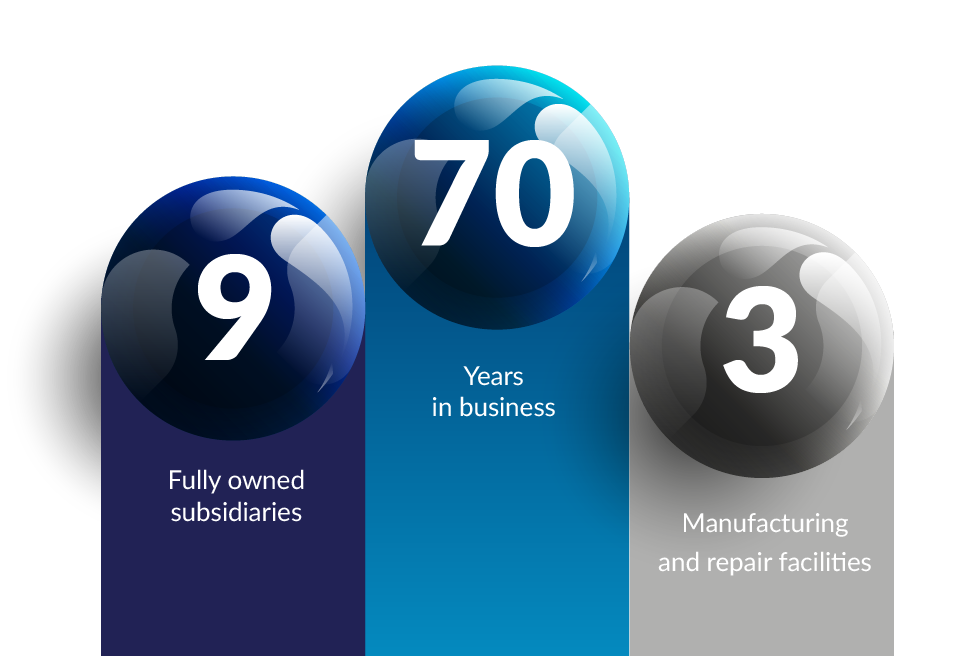
Our history
A track record of expansion and technological development
1954
SGM began with standard circular electromagnets for lifting scrap and plates, later developing new magnetic lifting solutions to meet the needs of more sophisticated mill applications, including slabs, billets, coils, multi-plates, rails, bundles of construction bars, structural steel, and pipes.
1974
The introduction of Electro-Permanent Lifting Magnets quickly gained users’ confidence and interest due to the enhanced safety they provide.
1991
To meet the oil industry’s evolving safety, performance, and weight requirements for pipe lifting applications on offshore drilling platforms, SGM introduced a new generation of Rare Earth Electro-Permanent Lifting Magnets. This advanced technology was soon adapted for various lifting magnet applications in the steel industry.
1993
Opening of SGM Germany, SGM UK and SGM Belgium
1995
Introduction of the first proprietary SGM Flux Measuring Device (FMD), a groundbreaking innovation in safety measurement technology for assessing the lifting force of magnets.
Opening of SGM Magnetics in Pittsburgh, USA
2003
Introduction of the octagonal SGM Mega Scrap Lifting Magnet, featuring a proprietary double magnetic circuit that enables the handling of more ferrous scrap in a more compact design compared to the traditional two large round magnet solution. These scrap magnets quickly became the benchmark solution for fast and efficient railcar loading/unloading operations and are particularly suited for belt loading with Consteel technology.
Introduction of the proprietary VHG Magnetic Circuit, which combines rare earth magnets (Neodymium) and ferrite magnets. This innovative design merges the deep but relatively weaker attraction force of ferrite permanent magnets with the very strong but shallower attraction force of rare earth magnets, optimizing magnetic performance.
2004
Introduction of the proprietary SGM Dynamic Ferrous Separators (DSRP), a technological evolution of traditional magnetic pulleys, enabling the segregation of sellable ferrous nuggets from magnetic waste.
2006
Introduction of the proprietary SGM Polishing Drum Magnets (PDM), designed to separate electrical rotors (commonly known as “meatballs”) from a ferrous scrap stream, thereby reducing the copper content in ferrous scrap.
2007
Introduction of the proprietary SGM Lifting Magnets for eye-horizontal steel coils (CDMD). The CDMD technology measures potential flexing and dynamic stress in the coils during handling, enabling greater safety and innovation in lifting magnet applications.
2008
Opening of a second SGM subsidiary on the west coast of the USA, Los Angeles.
2010
Introduction of the proprietary SGM Lifting Magnets with no side magnetic dispersion. These magnets are specifically designed for steel service centers, allowing them to enter racks of steel bundles without unwanted side attraction to steel columns or adjacent bundles/packs, ensuring precise and efficient handling.
Opening of SGM India disposing of a mechanical shop for both production and repair.
2011
Introduction of the proprietary SGM Eddy Current Separator (TVIS), spinning at 6,000 rpm and featuring a titanium protection sleeve to contain the centrifugal forces of the permanent magnet blocks. To this day, SGM remains not only the pioneer of high-frequency ECS technology but also the leading supplier, providing more high-frequency ECS units (ranging from 3,000 to 6,000 rpm) than all other brands combined.
Opening of SGM China with a demo line for the separation activity implemented in 2015
2013
Introduction of the proprietary SGM Scrap Cleaning Line for Heavy Melt Scrap (HMS SCL). This solution is designed to significantly reduce the approximately 5% non-ferrous contamination present in HMS, optimizing the efficiency of the electric arc furnace.
Introduction of the proprietary SGM MIMS (Medium Intensity Magnet Separator) for the iron ore mining industry. The innovative magnetic circuit of the SGM MIMS represents a true technological breakthrough in the field of magnetic separators for iron ore.
Introduction of the SGM X-Ray Dual Energy Transmission Sorter (XRT) for processing metals, heavy plastics, and minerals.
2014
Introduction of the proprietary SGM Smart Ballistic Separator (SBS) for processing Incinerated Municipal Waste (IBA). This separator enables the processing of wet IBA, the concentration of solid pieces—including metals larger than 2 mm—and the production of drier output compared to the infeed material. The SGM SBS represents a significant advancement in the performance of modern ballistic separators.
Introduction of the proprietary SGM Convection Electro Lifting Magnet (CELM) for hot materials. The CELM’s innovative design significantly extends duty cycles and lifespan when handling hot steel loads such as slabs and billets. The SGM CELM represents a revolutionary technological breakthrough in electro lifting magnet technology.
Opening of SGM Mexico covering all Latin America
2015
Introduction of the proprietary SGM Convection Electro-Permanent Lifting Magnet (EPCLM) for hot materials. Its innovative design significantly extends duty cycles and lifespan when handling hot steel loads such as slabs and billets.
Introduction of the SGM High Resolution Color Sorter (CSS) for metals, polymers,…
Introduction of the SGM Eddy Current Separator (BVIS), designed for the separation of ultra-fine non-ferrous metals down to 0.2 mm.
2016
Introduction of the SGM Air Classifier (ACL and ACS), specifically designed to optimize the separation time between light and heavy particles.
Introduction of the SGM fully in-house designed Induction Sensor Separator (EMS) for stainless steel and copper wires.
2017
Introduction of the latest generation SGM X-Ray Separator (XRT) for processing shredder residue fluff, designed to reduce chlorine and bromine content to less than 1% in over 70% of the fluff residue.
2018
Introduction of the SGM Multi-Beam Lifting Magnet Spreader Beams, designed for the quick and efficient switching between different magnet systems.
2020
Introduction of the SGM Extra High Gradient Magnetic Separator (SRP-W), specifically designed to remove weakly magnetic contaminants, such as stainless steel fragments, from a mix of ASR Insulated Copper Wires (ICW) sorted by induction sensor sorters.
2021
Introduction of the proprietary SGM AirMag Separator (AMS), which combines magnetic and gravimetric separation in a single sorter. Specifically designed to remove stainless steel contaminants from a mix of ASR Insulated Copper Wires (ICW) following a Pre-Chopping process.
Introduction of the SGM Refining Hammer Mill as a Pre-Chopper for ASR Insulated Copper Wires (ICW), enabling the processing of low-grade ICW.
Introduction of the SGM complete “No Blade” (no granulator) Insulated Copper Wires (ICW) chopping process, utilizing two turbo mills for enhanced efficiency and durability.
2022
Introduction of the proprietary SGM X-Ray Sorter (XRF-T), which combines both X-Ray Transmission and X-Ray Fluorescence technologies into a single sorting system.
2023
Opening of SGM Japan branch office.
2024
Strategic partnership with Cleansort GmbH for the marketing and servicing of the LIBS sorter.